This system is installed on the top of the blast furnace, and can measure the appearance of the material surface in real time during blast furnace operation. Compared with the existing commercial plug-in rod surface measurement equipment, this system has the advantages of air leakage, small size, and easy operation and maintenance. It is measured after each fabric of the blast furnace, so that blast furnace personnel can choose appropriate fabric operations based on the surface appearance information in real time, so that the furnace air is evenly distributed and the blast furnace operation efficiency is maintained.
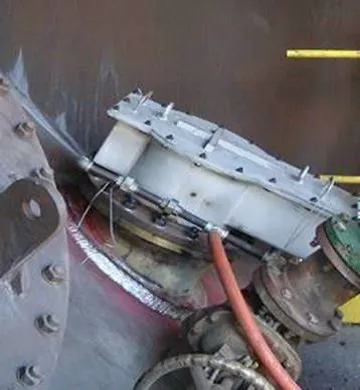
The shape of the material surface after the blast furnace fabric directly affects the flow of blower gas in the furnace. The uniform air permeability of the material layer can increase the thermal utilization rate of the reducing gas, increase the iron production, and reduce the furnace wall thermal load and increase the blast furnace life. Real-time fabric appearance can be used as a basis for adjusting the fabric angle and number of circles. However, the harsh environment of the blast furnace roof limits the application of measurement technology. China Steel successfully uses microwave ranging technology and combines the newly created scanning architecture to greatly reduce the system volume, making it the easiest and most stable system among the existing blast furnace resident surface measurement equipment.。
Residential installation: Fixed to the top of the furnace to avoid air leakage in the moving parts design, and to escape the measurement method of the traditional large measuring rod being pushed into the furnace from outside the furnace.
Ingenious design: Weight is about 160kg, installed on a 400A standard flange, does not occupy the furnace roof space and is easy to install.
Wide scan range: Each system scan range includes at least the material surface radius. If it is two opposite designs, the complete distribution of the material surfaces on the diameter can be obtained. The blast furnace does not need to suspend the fabric for measurement, and the measurement can be performed after each fabric.
Fast measurement speed: Generally speaking, the material surface scanning can be completed within 45 seconds, and measurement can be carried out before and after the fabric to analyze the material layer distribution.
Low cooling energy consumption: The nitrogen flow rate for cooling is only 30l/min to protect the system.
Function of material ruler: When the system does not measure, it can display the high changes in materials at specific locations.
1. Real-time measurement results are displayed quickly in graphs. It can be linked to the PLC feed signal and set the automatic measurement mode.
2. The historical measurement results can be displayed graphically or digitally, making it convenient for blast furnace personnel to compare and process.
3. The measurement results can be combined with process parameters (blowing conditions and fabric matrix, etc.) and stored according to customer requirements.
4. The system has a fault self-detection function.
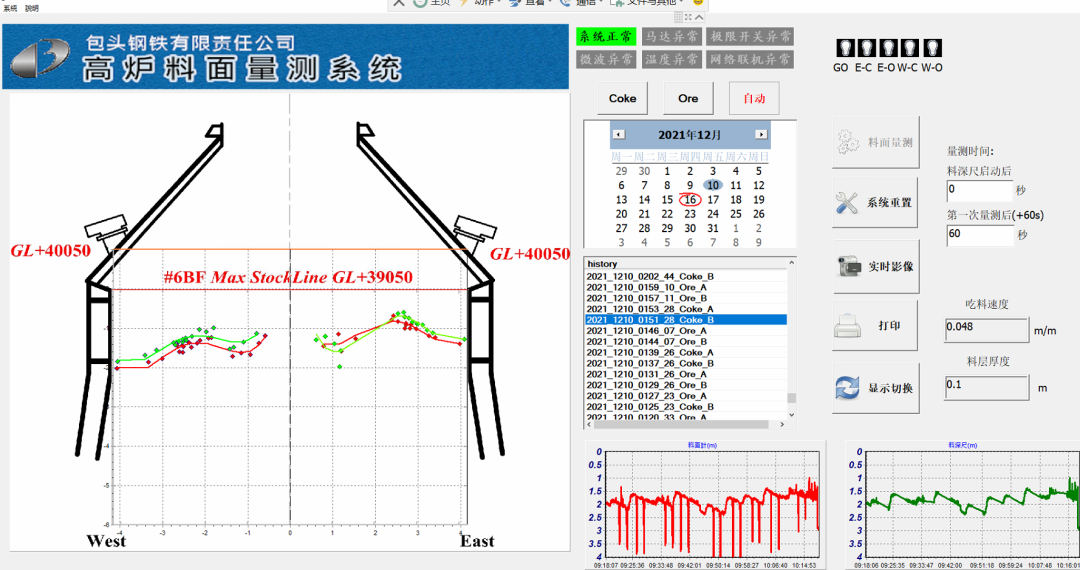
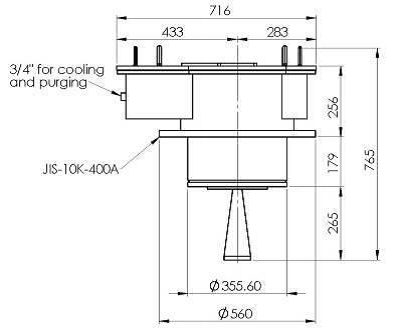
System application introduction
1. Use the surface shape (such as platform width and material depth) to evaluate and adjust the fabric matrix to increase the heat utilization rate of the blower gas and reduce the amount of coke.
2. When the blast furnace generates pipeline flow or slippage, the surface surface shape can be quickly restored through real-time measurement to stabilize blast furnace production.
3. Based on the continuous surface appearance measurement, it can be evaluated whether the furnace top discharge system is operating stably.
4. During the central focus operation, the formation of the central focus column can be confirmed and the size can be estimated to ensure the development of the central flow.